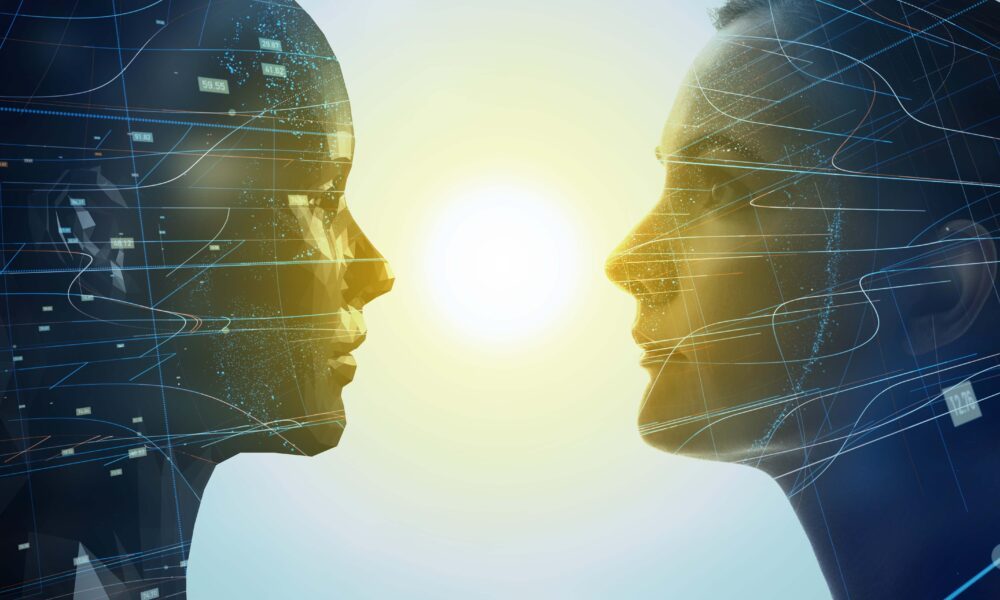
New technological advancements, such as robotics and Industry 4.0, are being introduced at a dizzying pace, which results in a constantly shifting manufacturing landscape. “Lights-out manufacturing” is among of the most frequently talked-about developments within the manufacturing industry, particularly in light of the precautions taken to combat the Covid-19 pandemic.
This concept denotes that factories continue to operate with automated manufacturing and few or no human laborers after hours. This is a revolutionary amalgamation of automated equipment along with digital assets that enhances efficiency and throughput while mitigating labor scarcity — if implemented properly.
Defining Lights Out Manufacturing
Lights out manufacturing is a method that employs fully-automated technologies to operate a production factory with minimal or no human intervention. Multiple technologies, like machine learning (ML), as well as high-frequency data acquisition, are required for this.
Lights-out manufacturing is additionally referred to as a “dark factory” because it operates essentially by itself, even in a factory that is otherwise vacant.
To accomplish this, businesses must automate each stage of the manufacturing process. This strategy is typically implemented by businesses with a technology platform consisting of machine vision, additive manufacturing machinery (3D printing), industrial IoT, peripheral computational resources, data stored on the cloud, ML, and robotics.
Why Adopt “Lights Out” or Fully Automated Manufacturing?
Many manufacturers have attempted to deploy a set-it-and-forget-it attitude to production. Simply report to work, activate the machinery, turn off the lights, and exit the building. No employees at all! There are no inhabitants on the premises.
Just machines completing what they can do so seamlessly: performing precise, repetitive duties much more quickly than their human counterparts.
This would significantly decrease incidents at work, the expenses incurred to keep the site adequately heated or chilled, and labor costs. Manufacturers would also experience fewer quality issues because, unlike humans, machines can precisely replicate their behaviors on a daily basis.
All of these 24/7 factories may sound like sheer fantasy, but they are currently and have been for many years a reality in manufacturing facilities across the globe.
Examples of Lights Out Manufacturing
Some of the most notable examples of manufacturers using automation to go “lights out” include:
- From the early 1990s until 2010, GE ran a light bulb facility in Virginia that generated over 10,000 units an hour with only a handful of human employees assigned to conduct machine maintenance.
- In 1980, IBM constructed a lights-out factory in Texas to assemble computer terminals. However, the initiative was terminated due to the plant’s inability to adjust to product variances due to the fixed tooling.
- Philips has been operating lights-out manufacturing facilities in the Netherlands to make electric razors with the assistance of 128 bots, along with only 9 quality assurance (QA) employees.
- Since the early 2000s, Fanuc has operated 22 lights-out factories that employ robots to build CNC machines. The robots can operate unattended with no maintenance requirements for up to a month.
In recent years, rapid advancements in automation and the Internet of Things (IoT) have made lights out manufacturing more viable at scale. Intelligent automation (thanks to artificial intelligence algorithms) have also helped since these systems are now more agile and flexible to change.
How Does Lights Out Manufacturing Work?
To understand how these fully automated industrial systems work, let us consider the example of a lights out warehouse in a manufacturing plant, where raw materials are stored after procurement.
The operations of the lights-out facility are carried out by automatic handling equipment, and it relies purely on automated logistics. It will be equipped with stacker cranes or mini-load systems (automated retrieval and storage systems for cartons). You can also anticipate internal products transport systems such as automated robots, conveyor belts, picking automation, as well as ops-managing automation software.
In this lights-out environment, all tasks, including the consolidation and deconsolidation of products, are delegated to automatic material handling equipment. In addition to various automated solutions, a lights-out facility may have unattended classification and vehicle loading/unloading mechanisms.
How to Implement Lights Out Manufacturing through Automation?
Recent advancements in digital technologies and manufacturing allow businesses to implement automated processes. Among the technological developments that have made autonomous production possible are:
- Breakthroughs in automation, industrial robotics, and 5G/6G networks
- New approaches to manufacturing processes like additive or 3D printing
- Advancements in automated non-destructive testing (NDT) to check materials
- Operational technology (OT) that can perform unattended assembly and production processes
- Cognitive technologies like artificial intelligence/machine learning (AI/ML)
- Augmented reality (AR) and virtual reality (VR) tools designed for manufacturing
Software is also essential to the effectiveness of lights-out deployments. For instance, manufacturing engineering software enables virtual simulation and design of automated operations. Consequently, you may verify them prior to investing in a production station on the shop floor.
The software for comprehensive manufacturing operations management (MOM) bridges the divide between digital design as well as actual execution. After planning and validating a lights-out work cell, a MOM framework manages manufacturing ops with automation in accordance with the plan.
Benefits of Using Automation for Lights Out Manufacturing
In hostile manufacturing environments, like those having oils and lubricants, corrosive chemicals, vapors, etc., complete automation can be an immense advantage. Industrial automation systems may be constructed with much more resilient parts — when compared to their human counterparts. Other key benefits include:
1. Reducing operational expenses
The reduction of operational expenses serves as one of the driving factors for automation. In the long run, robots can be more affordable than human labor despite their high initial costs. In addition, the drive for better minimum wages and perks for factory personnel is encouraging large corporations to increase their automation levels.
2. Pushing the need for operational uptime
Depending on the character or makeup of the production facility, unscheduled manufacturing delays can result in millions of dollars in missed revenues. Moreover, human inspection, maintenance, and repair (IMR) is the leading cause of intended manufacturing delays. To reduce downtime, businesses are eager to automate these duties and processes.
3. Coping with labor shortages
Manufacturers are experiencing labor shortages due to aging workforces and a dearth of recent college graduates. In addition, knowledge transfer and employee training for new employees are challenging and costly, making this a pressing need for automation.
4. Increase throughput
Machines are superior to humans at consistently carrying out repetitive tasks because they are not fatigued or preoccupied, and they can execute tasks with little variance for extended periods of time. Unlike human employees, a solidly constructed robotic system can operate nonstop without interruptions, vacations, or shift changes. This increased output can make robots more productive than human workers.
5. Scaling production to very large volumes
In certain circumstances, production volumes are exceedingly large, and human effort cannot meet the minimum requirement. These necessitate automation and dark manufacturing. This might be the case when millions of identical or only a few components are required, or when tens of thousands of evaluations are necessary.
6. Creating safer workplaces
In facilities that manage hazardous materials, employees are likely to sustain injuries. In manufacturing facilities with no lighting, the risk of injury is reduced. This means that businesses can reduce costs on premiums for insurance and other expenses related to providing employee health care benefits.
Conclusion: Pitfalls to Avoid on the “Lights Out” Automation Journey
Establishing fully automated processes may present a highly technical problem that requires a substantial investment. Furthermore, it may be more challenging to automate complex duties, or small-scale manufacturing lines and operations. Moreover, if anything does go awry, there might be no one to detect it, which could lead to additional expenses.
To navigate these challenges, manufacturers can start by automating selectively, with lights out work “cells,” which comprise a single, homogenous process that can be iteratively performed at scale. These lights out manufacturing cells can work alongside other automated or human-assisted units to form the right mix.